In the interest of reducing purchasing costs and streamlining storage and handling, many organizations have substantially slashed the number of lubricant SKUs (stock keeping units) they use. They have also re-engineered the precision of their lubricant specification. There are many real benefits to these consolidation initiatives if done correctly. Let’s go over some of the DO’s and DON’Ts of lubricant consolidation.
DO’S
DO Review each application for lubricant requirements and compatibility - When we recommend lubricants, we base the recommendation on several factors, one of the most important being the individual needs of each lubricated asset throughout the plant. This includes considerations such as viscosity for sufficient film thickness based on operating and environmental conditions. Additionally, compatibility with the current lubricant is important; a thorough flush may be required if the lubricant is incompatible.
DO Base all decisions on criteria such as volume, price robustness, and machine count - These are just a few factors that go into our lubricant recommendations. While cost justification is usually the most important factor in any facility, lubricant selection shouldn’t be based solely on the lubricant cost itself. Rather, it’s a cost-benefit justification, with long-term savings achieved from optimizing the selection.
DO Create a team of all stakeholders to be involved in the process - By stakeholders, we mean leaders: a team full of leaders that take ownership of the program. This may include participants from different departments, such as maintenance, operations, reliability, engineering, etc.
DO Ensure you have the correct amount of storage and handling devices to avoid mixing - The facilities we visit are often just starting their lubrication program. One of the main strategies we encourage is developing a proper reception and storage plan, including the proper hardware to maintain cleanliness, control quality and prevent cross-contamination (i.e., bulk oil storage, dedicated transfer pumps, etc.).
DO Set a review period every two years to ensure consolidation efforts are maintained - This is more of a QA/QC (quality assurance/quality control) check to stay on top of the program and ahead of the game. A lubrication program isn’t achieved; it’s maintained. This goes back to taking ownership of the program: continuous improvement is the name of the game.
DON’TS
DON'T Try to reduce to a single lubricant - This is why we prefer using the term “Lubricant Optimization” instead of consolidation. We are trying to reach a level where the facility will have a manageable number of lubricants while still covering the vast array of applicable ranges required to lubricate each asset properly.
DON'T Rely solely on the lubricant supplier to select lubricants - The lubricant supplier is sometimes unfamiliar with a specific plant’s needs and may recommend lubricants based on their experiences with other plants. I am not saying that the suppliers are out to ruin the program, but they don’t necessarily go into a high level of detail when making lubricant selections. On the other hand, they may not have a specific lubricant/additive package that meets the standards set by the Original Equipment Manufacturer (OEM) or the facility for a certain piece of equipment. If the incorrect lubricant is chosen based on a limited selection, it could cost the facility a lot of money down the road.
DON'T Select lubricants based on price alone - We all understand that cost is king. However, when we move past the initial sticker shock, having a generous budget for lubricants is paramount. What you spend on the correct lubricant will save the plant from having to spend an even larger amount of money when the machine goes down, especially when factoring in replacement and man-hour costs.
DON'T Buy tools or build a lube room prior to consolidation - Establishing a good lube room is the best foundation for a lubrication program. If this is done before optimization, you could easily overspend on storage and handling equipment when that spend has the potential to be greatly reduced by understanding the exact type and quantity of lubricant that will be used.
DON'T Add a lubricant for each new machine that’s installed - When selecting a lubricant for newly installed equipment, it's not uncommon to defer directly to the OEM’s primary recommendation. While this works, it does not satisfy the plantwide consolidation needs, and the problem will get worse with each new machine that gets added.
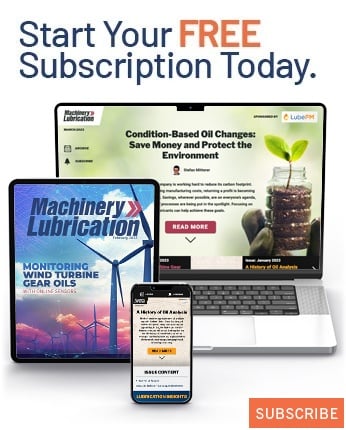